129 Life Is On | Schneider Electric www.se.com Chapter 2 – Sustainable development Strategic Report 2. Transition risks Schneider considers the possible financial impacts of future CO 2 costs on its activities, by taking into consideration both operational and supply chain footprints. Given the relatively low level of the Group’s Scope 1 and 2 carbon emissions, carbon pricing has indirect rather than direct impacts, resulting in increased supply chain costs, especially regarding the purchase of raw materials and manufactured components containing metals and plastics. A carbon tax at EUR 50/tonne of CO 2 is estimated to have an impact on the Group’s industrial supply chain up to EUR 420 million globally (including direct and indirect impacts). Climate change mitigation will likely lead to regulation strengthening, which can disrupt markets. For instance, SF 6 -insulated switchgear can have a significant impact on climate change if SF 6 is mishandled at the end of life of the equipment and leaks into the atmosphere. Schneider Electric strives to anticipate regulation changes and launches innovative SF 6 -free solutions. Workplace disruptions Extreme weather events, floods, droughts, and other climate impacts will increasingly put pressure onto supply chains. Shortages of all kinds can translate directly into revenue loss (missed orders), increased costs (urgent shipping), and increased working capital requirements (stock management). Extreme events can also cause damage to property and assets. This risk can be mitigated by adopting a flexible and resilient supply chain, with the ability to rebalance supply and manufacturing. To further tie climate-related issues to financial planning, Schneider successfully launched the first-ever sustainability-linked convertible bonds in 2020. This bond has been linked to three SSI targets by including the objective to save and avoid 800 million tonnes of CO 2 on the customers’ end by 2025. 2.3.1.3 Risk management Risks are identified and assessed through specific internal and external metrics, but also through interviews with experts and leaders, run by the Internal Audit Department and the Group Risk Management Department, to update the list of general risks at Group level each year. In 2021, around 40 of the Group’s top managers were interviewed in addition to Board members. Environment and climate-related risks are included in Schneider’s unique risk taxonomy (more details in Chapter 3 “How we manage risk at Schneider Electric”). Every three years, a materiality analysis is conducted by the Sustainability department, leveraging an external consultant, and complements the risk analysis with a focus on environment, social, and governance (ESG) topics and longer-term risks and opportunities (more details in section 2.1.6 “Main ESG risks and opportunities”). Overall, the different governance bodies involved in the definition and monitoring of the sustainability commitments and programs (SSI and SSE), and in particular the Carbon Committee, are in charge of defining strategic mitigation programs in response to the risks and opportunities identified. Strategic programs defined at Group level are then cascaded into business divisions, down to the sites for implementation, and are monitored through the digital platform, EcoStruxure ™ Resource Advisor. Performance against those programs is published quarterly in the Schneider Sustainability Impact (SSI), and annually in the Schneider Sustainability Essentials (SSE) and Universal Registration Document. Each program of the SSI has a dedicated pilot in charge of driving the transformation, and is sponsored at the Senior Vice-President and Executive levels to ensure management control and oversight. Climate adaptation risks are also studied and mitigated at site level for the industrial sites. The Group’s Property Damage and Business Interruption program, inspired from ISO 22301 standard, maps substantive risks of financial impact on the business, including asset destruction (buildings, equipment, inventories) and profit loss due to business interruption. The program reviews annually the natural hazard exposures of our manufacturing and logistic locations. An example of a risk analyzed at site level is flooding risks. Risk analysis of industrial sites includes an analysis of interdependencies, study of alternative supply, and estimation of time to recover in case of damage, etc. Typically, all critical industrial sites are externally audited onsite at least every two years. In addition, starting 2021, Global Supply Chain has defined a resiliency index to assess and mitigate business interruption risks. This resiliency index covers several risks (such as physical security, political stability, etc.) and includes exposure to natural and climate-related hazards and mitigations. Finally, environmental risks (including climate) are assessed and mitigated at site level through the Group’s Integrated Management System (IMS). The IMS covers the supply chain sites (plants, distribution centers, large offices) and hosts ISO 14001, ISO 50001, ISO 9001, and OSHAS 18000/ISO 45001 compliance management systems. Each site is audited periodically, either externally by Bureau Veritas (every three years), or internally. At present, the impact of climate-related matters is not material to the Group’s financial statements. With suppliers, sustainability risks (including natural and climate- related hazards), are embedded into Supplier Risk Assessment. This process enables to define risk mitigation action plans with suppliers, as well as prioritize double sourcing strategies. Leveraging external data providers, the Group monitors events across 10,000 nodes (such as ports and critical supplier locations) to shorten reaction time when events occur and minimize business impact.
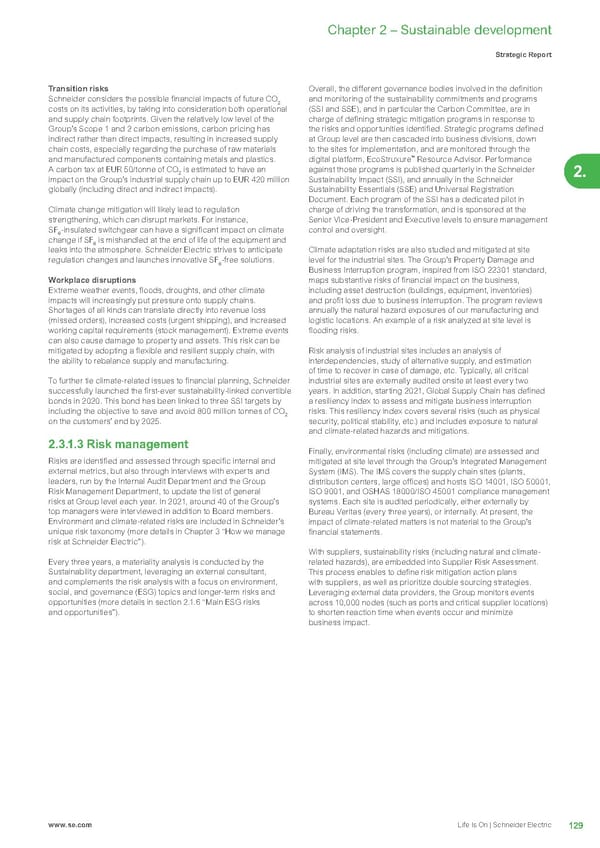